Specialized Large Pipe Bending Machine
The large pipe bending machine has been specifically designed to meet the demands of precisely processing large, thin-walled pipes. It consists of a vertical holding press and a horizontal pushing press, which together provide a powerful and efficient solution for the complex bending process. This combination of technologies allows for the accurate bending of large pipes without compromising the integrity of the material. This is particularly important for applications where material quality and dimensional accuracy are critical.
A standout feature of this specialized machine is its ability to bend thin-walled pipes into precise 90° bends through a complex forming process. This is achieved while maintaining a relatively small internal radius, which is particularly challenging given that thin-walled pipes are prone to deformation or damage during bending. This challenge is overcome through the high pressure and precise control of the system, ensuring that the material maintains its original quality and shape. The achieved dimensional accuracy and tight bending radius ensure that the final product meets the highest standards.
Technical Data of the Machine:
- Pressure capacity of the vertical holding press: 20,000 kN
- Pushing force of the horizontal pushing press: 5,000 kN
With this combination of high pressure and pushing force, the machine can achieve both complex and difficult forming processes with high efficiency and precision. This is especially critical in the processing of large, thin-walled pipe materials used in extreme conditions, where precision and material integrity are paramount.
The large pipe bending machine is primarily used in industries that require the highest standards of product quality, reproducibility, and safety. These include the aerospace, automotive, and energy industries, where pipe systems must not only be functional but also safe and durable. Pipes in these industries are often used in critical applications where they must withstand high loads and extreme conditions. In these cases, precise bends that do not cause material fatigue or structural weaknesses are of the utmost importance.
Another advantage of this machine is its versatility in processing various pipe materials and sizes. From specialized alloys to large pipe diameters, the large pipe bending machine can be adapted to meet a wide range of production requirements. This flexibility ensures that the machine can accommodate a broad spectrum of applications and is suitable for companies that need to process a variety of pipe types in their production lines.
The forming process is optimized through the advanced control technology of the machine, which enables continuous monitoring and adjustment of process parameters. This ensures consistently high product quality and minimizes scrap. The control systems ensure that the forming forces are applied evenly and precisely to the material, which is critical for the quality of the bend and the integrity of the final product.
In addition to precision, the efficiency of the large pipe bending machine is also noteworthy. By combining high-performance components with intelligent control, the production process is accelerated, leading to higher throughput rates and lower operational costs. This allows companies to produce large pipes more quickly and cost-effectively without compromising quality or safety.
This specialized machine not only increases production capacity but also reduces material waste and downtime. It enables the mass production of high-quality, precisely bent pipes that meet the rigorous demands of the most challenging industries.
In conclusion, the large pipe bending machine represents an innovative solution for processing large, thin-walled pipes, meeting the highest demands for precision, quality, and efficiency. It plays a vital role in the manufacturing of components used in critical industries such as aerospace, automotive, and energy, offering a future-proof technology that will continue to meet the highest standards in pipe forming technology.
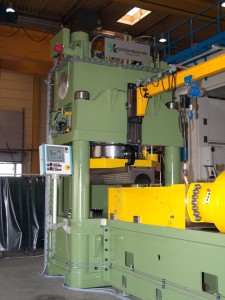
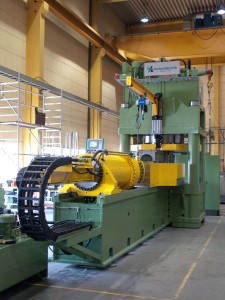
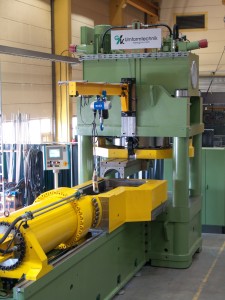
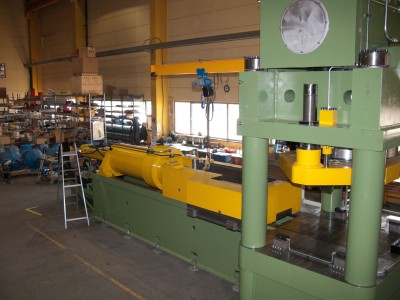