What is a four-column press?
A 3- or 4-column press is a hydraulic press where, as the name suggests, the force is applied within a closed frame consisting of a top plate, a bottom plate, and the columns connecting them. These columns serve as the supporting structure and absorb the tensile forces during the pressing process. Column presses are available in various sizes and configurations. Symmetrical loading is crucial, as the columns are not capable of handling asymmetrical loads or counteracting resulting torsion.

Column Press
Workshop press for single part manufacturing and small series production
Application Area
The G+K four-column press is frequently used for applications such as tool testing presses, single part manufacturing, or small series production. It is also used in large-scale production as a deburring press (e.g., to remove casting burrs) or in cases where minimal space is required while maintaining high tool accessibility (e.g., for robotic removal). The four-column design is particularly suited for these applications.
Special Features of G+K
The massive top and bottom plates provide stability to the machine. The columns are fixed in place without stress. The ram is precisely guided on a long guide using round guides.
Control
Siemens S7-1500 series; control panel depending on functionality, Siemens Comfort Panel Control elements: Two-hand control, light barrier control, and for tool testing presses, also with a sensitive joystick.
Customizable Parameters of Our Column Presses
Force, Stroke Length, Installation Height
The basic dimensions are the pressing force, as well as the measurements between the top and bottom dead centers, and between the table and the ram at the top dead center (TDC).
Table Size
Table width in mm x table depth in mm. The arrangement of grooves in the table and ram is important for the planned tools. The space between the columns can also play a significant role.
Working Area/Table Size and Ram Area
The dimensions of the working area or the table, and the ram where the tool is mounted. These are specified in width x depth.
Speed
Speed of rapid traverse, working speed, and return speeds are determined during the initial press design.
Tool Change System
Tool changes are significantly simplified using hook-on supports and ball or roller rail elements. Hydraulic clamping elements also significantly reduce setup times.
Safety
The sides are closed with protective grids by design, and a protective door secures the rear part of the press. At the front, there is either a light curtain or a mechanical protective door that eliminates the risk of operator injury.
Which type of press is right for my application?
Presses can also be distinguished by the geometric shape of their frame. There are single-column presses, also known as C-frame or swan-neck presses, double-column presses, also called H-presses, as well as three-column and four-column presses. Depending on the structure, the machine’s deflection or elongation varies, which in turn affects the achievable precision of the end products and the wear of tools. The machine’s design also impacts accessibility to the press table, setup times, and required safety features, such as non-contact protective devices.
Advantage "Tool Testing Press"
Due to the excellent visibility between the columns, this press is ideally suited as a tool testing press. Using a joystick, the ram is moved with great sensitivity, allowing everything to remain in view during the tool closing and adjustment process, preventing any unintended damage.
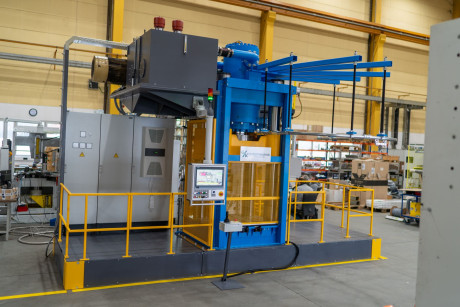
Would you like to learn more about our Four-Column Presses?
How could you find the perfect-fitting Four-Column Press?
- Your task, our concept
- Sizing and layout
- Discussions with your practitioners and our developers
- Budget proposal for your planning
Feel free to contact me to schedule an appointment regarding Four-Column Presses.
